Modelling of melt motion
The goal of the project is to identify the principal physical mechanisms of melt motion, surface deformation and droplet ejection in contemporary fusion devices as well as in future fusion reactors but also to provide qualitative predictions for ITER and DEMO.
The provision of plasma-facing components (PFCs) with sufficient lifetime is one of the primary technological obstacles to be overcome in the development of commercial fusion reactors. In fact, for next generation tokamak devices such as ITER (currently under construction) and DEMO (currently in the planning phase), the PFC lifetime & power handling capabilities constitute major design challenges. ITER features a beryllium (Be) first wall and a full tungsten (W) divertor. In the divertor, intense steady state heat loads will elevate surface temperatures close to or above the recrystallization range of W, raising concerns for edge melting and even full surface melting due to additional fast transient power loading during downward vertical displacement events (VDEs), edge-localized modes (ELMs) or loss of detachment control. On the main chamber, the principal concern is the thermal and current quench phases of unmitigated VDEs or major disruptions. In fact, key aims of the Pre-Fusion Power Operation phase of ITER reflect the above since they include the demonstration of effective disruption mitigation and reliable ELM suppression. Nevertheless, some PFC melting appears to be inevitable; the Be wall is already at risk during early ITER plasmas at low plasma current, while melting in the W divertor becomes a risk later in the ITER operational stages, when the stored plasma energies are higher.
Metallic tokamak melts are subject to strong electromagnetic forces that displace the molten material and cause large-scale surface deformation, thus severely compromising power handling by modifying the incident magnetic field angle. Severe melt motion could also bridge castellations or even lead to the release of large droplets. The main concern is the overall material excavation which may ultimately necessitate the costly replacement of damaged components. Hence, reliable assessment of the extent and possible consequences of melt events are crucial for ITER and beyond.
The study of melt events induced by transient heat and current loads requires the treatment of free surface magneto-hydrodynamic flows with phase transitions. These are fundamentally multi-scale phenomena with order of magnitude differences between the tangential liquid metal extent, the melt depth and the characteristic scale of non-linear free-surface instabilities (eventually responsible for splashing). Fully self-consistent numerical models in principle need to account for the intricate coupling between fluid dynamics, heat diffusion, phase transitions, current propagation into the PFC bulk and interactions with the plasma (in case of strong vaporization).
The project is focused on the development, validation (comparison with experiments in contemporary fusion devices) and application (predictions for different ITER and DEMO scenarios) of numerical tools for the modelling of macroscopic melt motion with large displacements – the MEMENTO code – as well as for the modelling of strong free-surface deformation and melt splashing – currently with customized set-ups in the ANSYS fluid dynamics software suite.
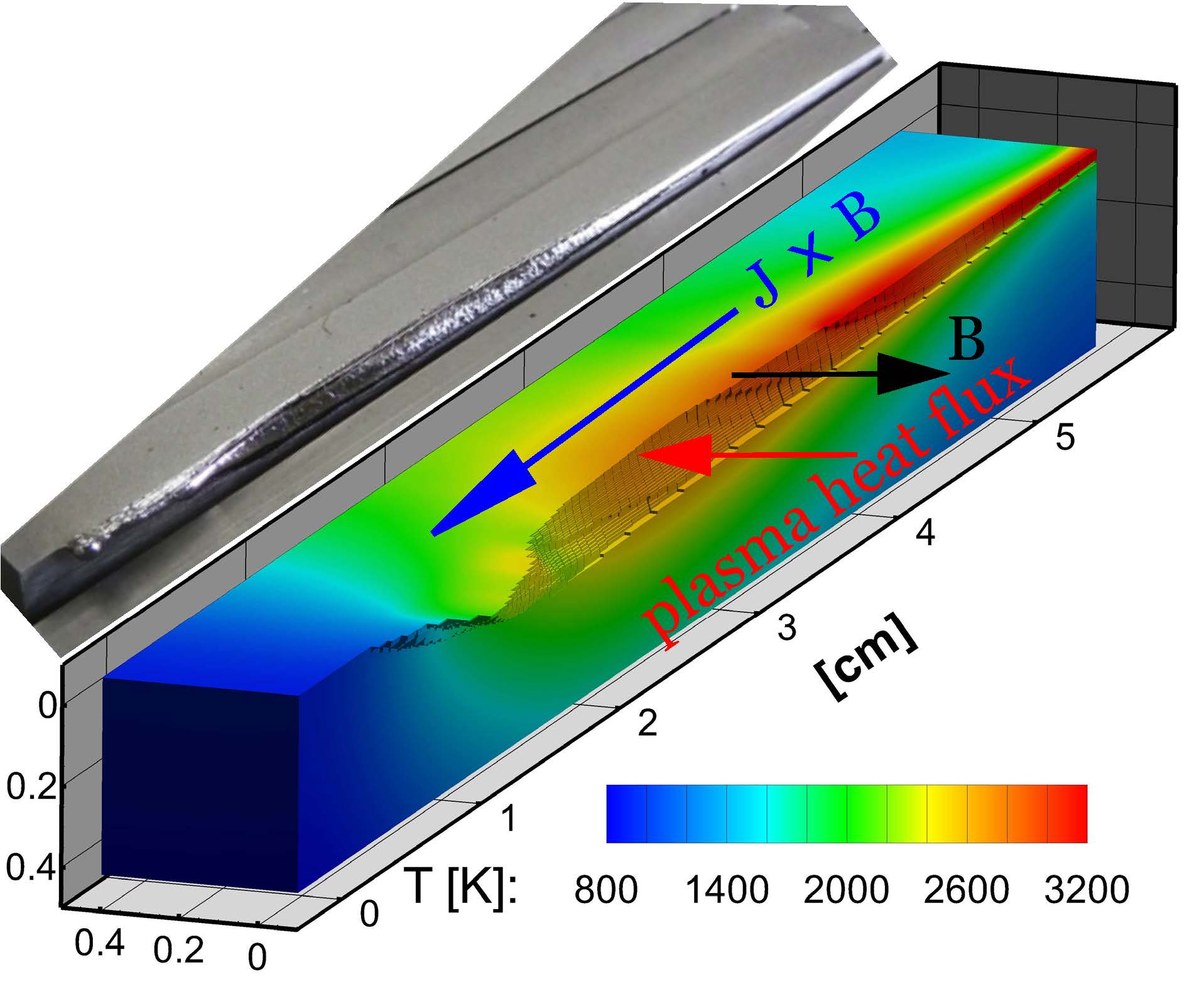
MEMENTO, a new realization of the physics model of our MEMOS-U code, solves the incompressible resistive thermoelectric magneto-hydrodynamic equations in the magnetostatic limit for uniform materials, together with the heat convection-diffusion equation. It utilizes the shallow water approximation (obtained by integrating the Navier-Stokes equations across the liquid depth), which drastically decreases computational costs by reducing the dimensionality of the fluid equations by one; this makes it a suitable tool for parametric studies. Boundary conditions, such as the incident heat flux and the surface current density constitute external input. The MEMENTO code utilizes non-uniform and adaptive meshing along with sub-cycling in time enabled by the AMReX open-source framework as well as by AMReX's built-in parallelization capabilities. The physics model has been extensively tested against dedicated state-of-the-art experiments in the ASDEX Upgrade, JET and WEST tokamaks. The exposures involved different plasma states (L-mode discharges, Type-I ELMing H-mode discharges, upward VDEs, runaway electrons), different exposure geometries (leading edge divertor plates, sloped divertor plates, upper damp plates), different material composition (tungsten, beryllium, iridium, niobium), different electrical connections (grounded, floating) and different cooling channels (passive via thermal radiation, vaporization and electron emission, active via water coolant). Successful reproduction of the experimental results demonstrated that the model adequately accounts for the essential physical processes at play. Being validated and computationally efficient, the MEMENTO code (and its predecessor MEMOS-U) is exclusively employed for melt damage predictions in ITER and DEMO.
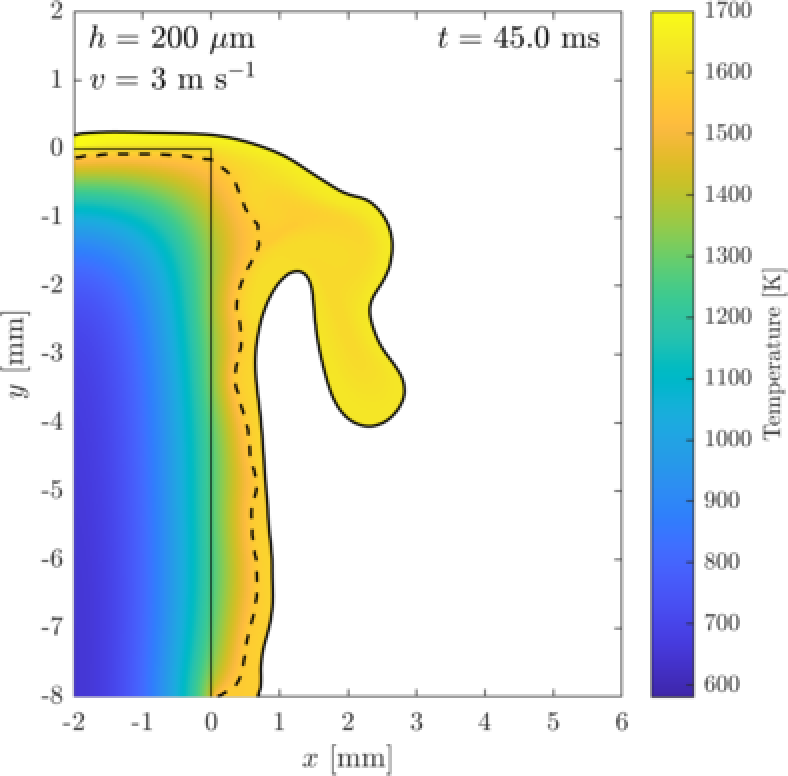
Smaller-scale flow features such as strong free-surface deformations and melt ejection are simulated with customized set-ups in ANSYS that solve the coupled multi-phase Navier-Stokes and heat equations using the volume-of-fluid method, with plasma heat and momentum drive as boundary conditions. Successful benchmarks against published simulations of pressure-driven melt ejection from copper cathode spots in vacuum arcs have been performed, as well as initial validations against direct measurements of droplet size and speed distributions. In addition, simulations of liquid Be flows over the straight edge of plasma-facing components have been carried out in conditions emulating the upper dump plate melting observed experimentally in JET. Comparison of the numerical output with JET data, regarding the morphology of the frozen melt layers and the location of Be droplets splashed onto nearby vacuum vessel surfaces, confirmed the predictive capabilities also of these set-ups.
Funding agency: ITER – KTH Implementing Agreement (IO/IA/16/4300001384), ITER contract (IO/20/CT/4300002230), ITER – KTH Implementing Agreement (IO/IA/22/430000xxxx), VR 2018-05273 , VR 2021-05649 , Horizon 2020 EUROfusion Consortium 633053, Horizon Europe 101052200 EUROfusion
Former PhD students: Federico Lucco Castello, Emil Thorén
External Collaborators: Richard Pitts, ITER Organization – Karl Krieger, IPP, Garching, Germany – Luca Brandt, KTH, Sweden – Igor Kaganovich, PPPL, Princeton, USA – Andrei Khodak, PPPL, Princeton, USA