Perfecting the chemical transformation of biogenic waste into valuable products
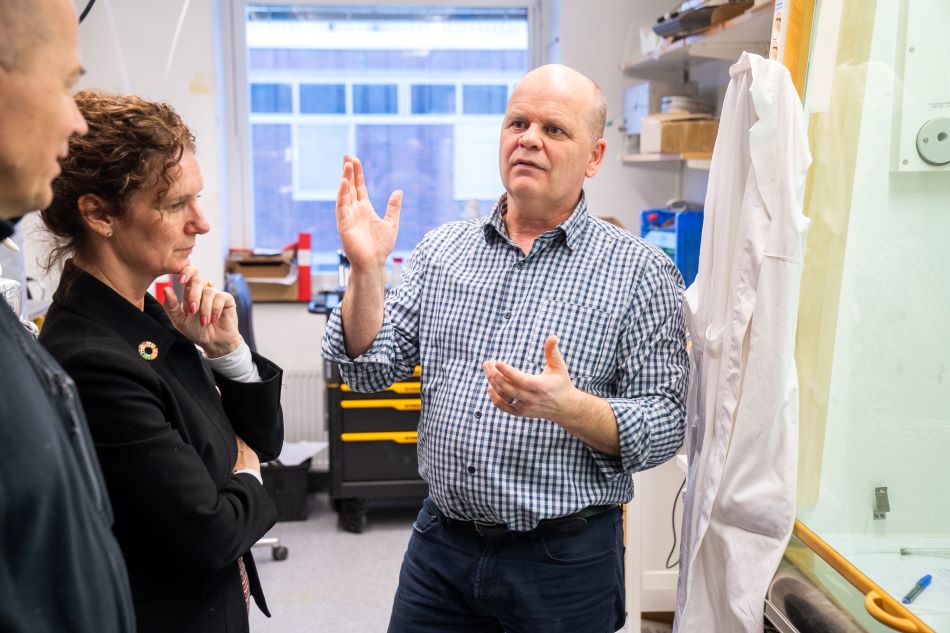
KTH Energy Platform’s last school visit of the term was to the Department of Chemical Engineering and the Division of Process Technology, which focuses on chemical energy and fuel conversion based on unique competences and experience from biogenic waste and biomass conversion. The Division also has a world-unique facility for pressurised fluid bed gasification.
KTH Energy Platform Director, Lina Bertling Tjernberg, Deputy Director Christophe Duwig, and Pierre Bodin, Research Advisor for Strategic Initiatives, all participated in the visit. They were welcomed by Klas Engvall, Director Division of Process Technology.
Research at the Division is focused on chemical energy and fuel conversion, with its main focus areas including industrial and environmental catalysis and thermochemical conversion of biomass and biogenic waste. Interest in producing biofuels and chemicals from biogenic waste is growing, especially internationally. Research in these areas also faces challenges associated with developing new processes that contribute to the circular and sustainable society of the future.
The first stop on the visit was the Division’s smaller reactor for combustion, gasification and pyrolysis, which was currently being rebuilt. Research engineer Christer Rosén explained how the reactor works. He has been tasked with ensuring that the reactor is equipped with a variety of functions, including a new control and regulation system.
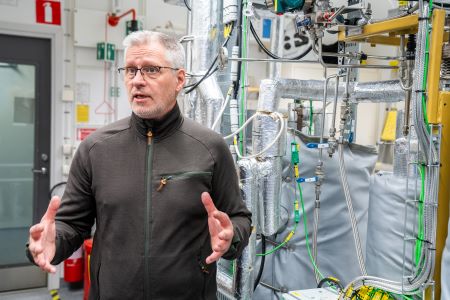
The set-up is mainly used for pre-studies and simpler investigations for projects that are later carried out in a larger facility at the Division. It is also used by the Division’s doctoral students.
Engvall spoke about how first conducting smaller trials offers researchers a more cost-effective way of working.
“Our research is extremely costly, so we work very actively to find new ways to make it more cost-effective, including using components and instruments for our experimental equipment that are widely available in industry,” says Engvall.
One of the Division’s planned projects will be conducted in collaboration with energy company Stockholm Exergi, with the goal of understanding the breakdown of PFAS in wastewater sludge during incineration while recovering phosphorus. Other projects in the planning phase relate to recycling metals from residual products from aluminium production.
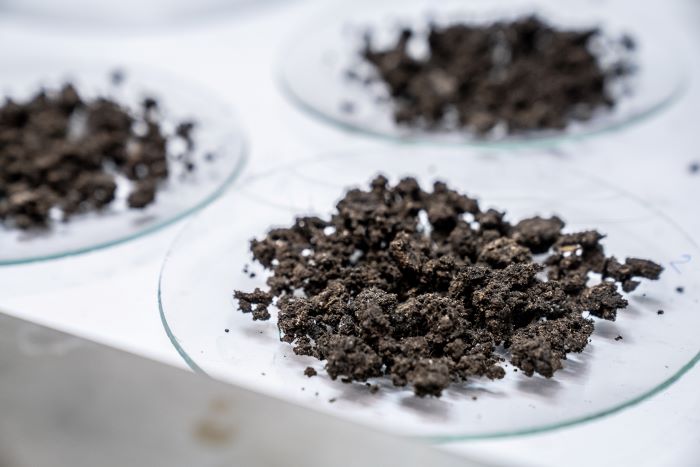
The Division’s research group for thermochemical conversion of biogenic waste runs several industrial collaborations, including with PyroCell, Meva Energy, and Phoenix BioPower. Together with Meva Energy, the researchers hope to study ways of using residues from furniture manufacturing at IKEA’s factories in Poland to generate electricity. The researchers also participate in several EU-backed projects around Europe, including WASTE2H2: Waste to Hydrogen and Bio-Flexgen .
Engvall is currently working on applying for a new national centre for thermochemical conversion in collaboration with Luleå University of Technology and a number of companies, including SSAB, LKAB, Uniper and existing business partners. This is also intended to bring the costs of research down with more people contributing to joint projects.
One of the Division’s doctoral students, Elise Farah, who was one of the 2022 KTH Energy Dialogue poster competition winners then took the lead. Her research focuses on refining residues from forest felling into new biofuels, for example, with the help of pyrolysis. The process includes the creation of a type of bio-oil, which, after further processing, could become the basis for both new paints and plastics.
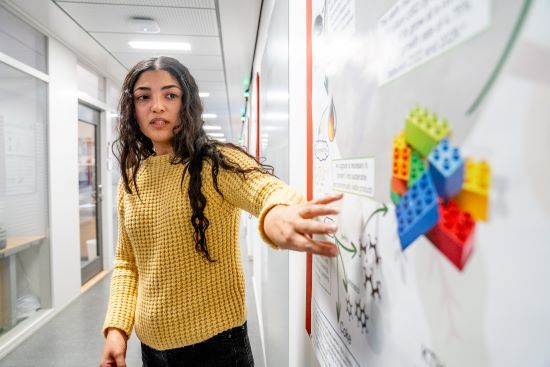
Today’s plastic materials are difficult to recycle because they consist of several different materials. However, the plastic materials resulting from Farah’s process can be used in a circular recycling process.
Next, doctoral student Tzu-En Chien and postdoctoral student Franziska Dahlman demonstrated a newly built instrument for investigating chemical surface reactions at the atomic level using lasers. The reactions take place at incredibly high speeds, which puts huge demands on the instruments used, so the researchers have built them themselves. Measurements are taken in a vacuum or pressure close to atmospheric pressure. Reactions are being investigated in which hydrogen reacts with another compound to enable storage in liquid form.
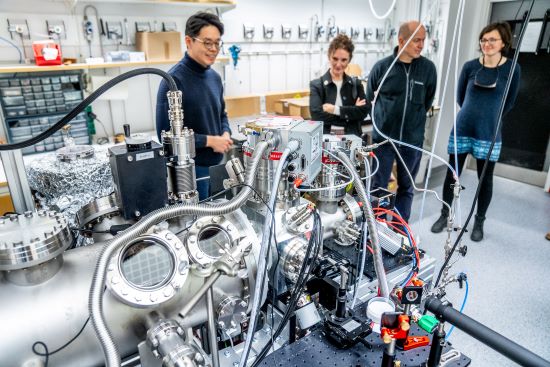
The aim is to see what happens in as much detail as possible and in as short a time as possible. The instrument makes it possible to capture how atoms behave on the surface of various materials in video film.
The project has funding from SSF and you can read more about it on Associate Professor Daniel Harding’s web page . You can see more images of the instrument on Tzu-En Chien’s Instagram account .
The last stop on the visit was the Division’s largest facility. The only one of its kind in the world that makes it possible to study thermochemical conversion at high pressure and temperatures. The equipment is able to withstand pressure of up to 30 bar and temperatures of around 1000 degrees Celsius. It consists of a number of reactors across three floors in a large industrial hall, surrounded by stairs and scaffolding.
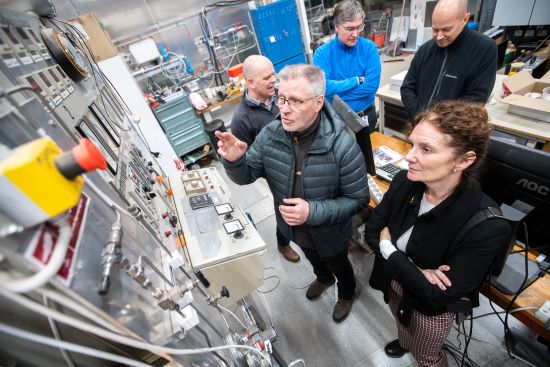
Research conducted here will map what happens during gasification and pyrolysis of different materials and combinations of materials, such as sorted industrial waste and different types of biogenic waste, and what can be recovered from these processes.
The equipment is also currently being rebuilt in preparation for trials with a new form of catalyst. The rebuild will be completed in the spring, when it will be ready for new experiments. When the reactor is running, the temperature around the equipment rises to 35-40 degrees Celsius, making it a tough working environment. During the spring, approximately 20 tests are planned, with each test taking up to three days to complete.
Text: Magnus Trogen Pahlén