Materials Design project: Advanced Stainless Steels
The goal is to avoid precipitation of harmful phases during production and manufacturing, while maintaining corrosion resistance and mechanical properties.
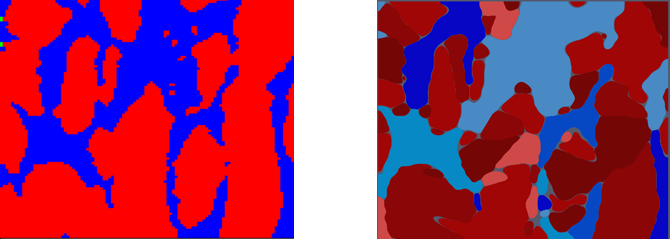
Duplex stainless steels derive their excellent corrosion resistance and mechanical properties from a microstructure which is composed of roughly equal amounts of austenite and ferrite. During production and subsequent welding there is a risk for precipitation of carbides, nitrides and intermetallic phases, all of which are detrimental for the final properties of the material.
An important corrosion type is pitting corrosion and a measure of an alloy’s resistance to pitting corrosion is given by its PRE (Pitting Resistance Equivalent) number. In theory it is easy to increase the PRE; one just adds more chromium, molybdenum etc. to the alloy, but in practice this inevitably leads to a material with less structural stability e.g. higher chromium and molybdenum contents increase the risk for forming the brittle unwanted sigma phase. The sigma phase is devastating for the impact toughness and the corrosion resistance is also adversely affected. Now, there is a demand for a hyper duplex stainless steel (PRE ≥ 50) with an increased structural stability but with maintained mechanical properties and corrosion resistance.