CBH researchers produce aerogels from nanofibers – in an ordinary freezer
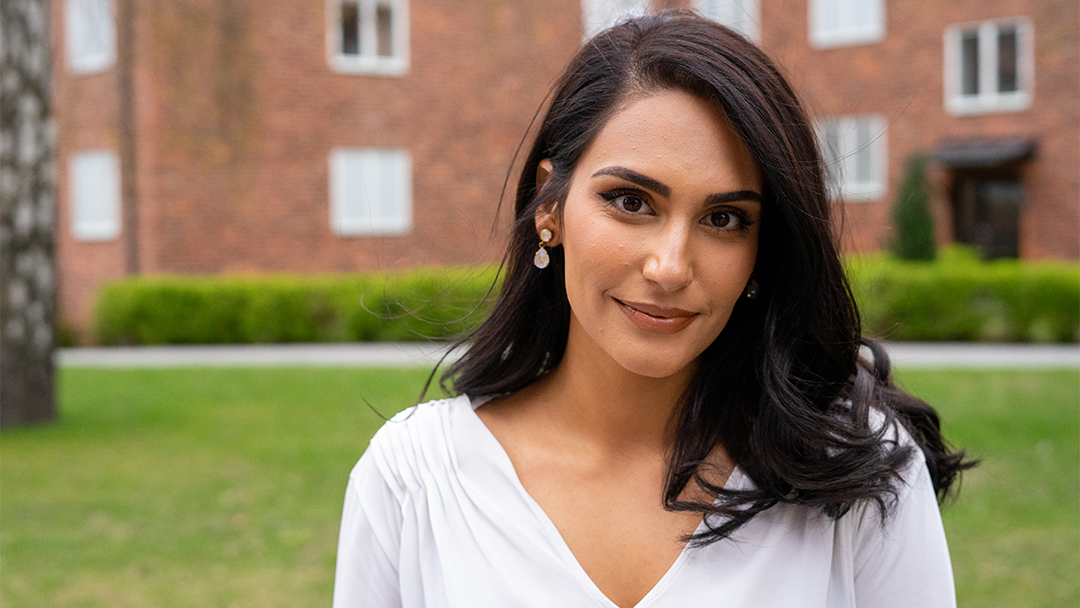
Jowan Rostami, doctoral student in fibre technology at KTH, has developed a simplified and environmentally friendly method for producing nanocellulose-based aerogels. According to the researchers, the material can be used in a number of biomedical applications, such as smart wound dressings.
“I have focused on making very light materials called aerogels. They are very porous and can be used in many different applications, such as absorption materials, in batteries and in biomedical applications, to name a few. It was fun that we managed to make very wet-stable aerogels from nanocellulose, alginate and calcium carbonate particles, through a sophisticated water-based method, and showed the potential of bio-based and renewable raw materials,” says Jowan Rostami.
Environmentally friendly production
Normally when creating aerogels, you have to use expensive and resource-intensive processes to produce such light 3D materials. But Jowan Rostami and the other researchers used regular freezing in a minus 18 degree freezer, similar to the one you have at home in the kitchen.
“Then we did something called solvent exchange, where you replace the aqueous phase with acetone (in this particular case), which could evaporate away. So it was a very simple procedure. What makes the process so sophisticated, is the fact that we use a little acetic acid in the acetone. In this way, the acid can dissolve the calcium carbonate particles, which release CO2 gas that can bubble through the structure and possibly give more porosity, while calcium ions are released and can cross-link the network and give us wet strength.
The researchers' aerogel has a high porosity of almost 99 percent and they managed to reduce the density to 2 kg/m^3 (the density of air is 1.23 kg/m^3). In addition, the material has good mechanical properties and good wet stability. The results have been published in the journal Materials Today . In addition to Jowan Rostami, the study was led by researchers from the Department of Technical Mechanics at KTH and the Department of Solid Mechanics at Lund University.
According to the study, the researchers' aerogels was functionalized using Metal-organic frameworks (MOFs), which have a very high specific surface area and can be integrated with various components such as DNA, protein and viruses.
“In our case, we had proteins that were encapsulated in the MOFs, which in turn were encapsulated in the aerogel, all according to a hierarchical structure. We showed that you can use this for biomedical applications by having a controlled release of the proteins. The proteins can thus be released with the right stimuli; if, for example, it is a slightly more acidic environment. So you could, for example, apply the same principle to wounds and get a very controlled release of medication over time,” says Jowan Rostami.
Showing the material’s potential
What do you hope this can lead to in the long run?
”You can achieve a lot with nanocellulose and different types of wood-based materials, but in terms of application, I think there is room in the industry to show the potential of nanocellulose-based aerogels, even for more advanced purposes. With this work, I hope that you can see that it is possible to tailor the properties and structure according to need, as well as the opportunity to further functionalize to use the materials in the application you have in mind. All this as sustainable and green as possible, mainly in water and other green solvents, and by minimizing energy- and time-consuming processes.”
How did you get caught up in this area of research?
"We have a lot of wood in Sweden and I think that this resource can with advantage be used in more advanced applications and materials. I think that the idea was fun, to take something that we have so much of and that is bio-based, cellulose from trees, and achieve things that you do not believe or expect to be able to make from this raw material. But as my main supervisor Lars Wågberg always says, you have to understand what you do and really focus on the fundamentals as well. So in addition to developing materials and testing different applications, I think it is rewarding that we really study and try to understand the interactions that are dominant in our network and what it means for the final properties of the material. After all, it is all this knowledge that has given us the opportunity to tailor our material and get such fine properties,” says Jowan Rostami.
Text: Jon Lindhe