Manufacturing and processes
Composite forming simulations are performed to predicting wrinkle development and fibre angle deviations during multi layer forming of thermoset prepregs.
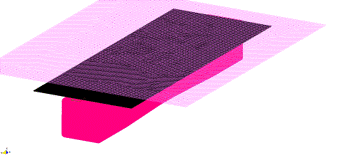
Material models describing intraply shear and interply shear characteristics are developed depending on material system used, forming pressure, speed and temperature.
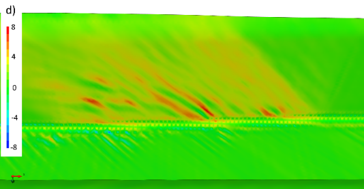
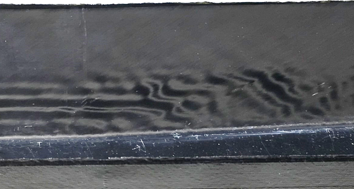
Simulation vs. real component at inner flange.
Automation and process control
Methods for automated forming using robot is researched. This technology enables steering the forming sequence into preferred order, suggested from simulations, thereby providing good quality of formed composite material.
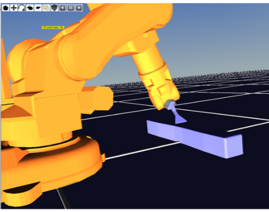
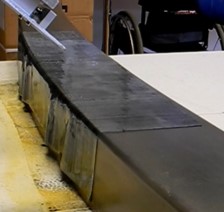
Heat transfer modelling
Heat transfer modelling plays an important role in the development of efficient composite manufacturing processes, e.g. when predicting optimal local temperatures during forming. It been shown that tailored forming temperatures differing over the surface of the material in order to reduce processing time and improve quality of formed component. In particular radius thinning is reduced.
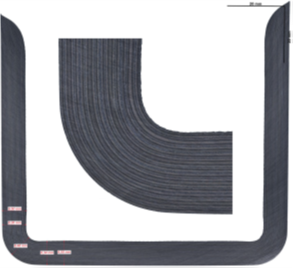
Shape distortions
Composite structures undergoes shape distortions during curing and cooling due to its anisotropic nature. Shape distortions of stiffened composited structures is studied in different PhD projects and model development is performed. Example of studies include composite forming and curing tools.
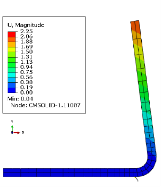
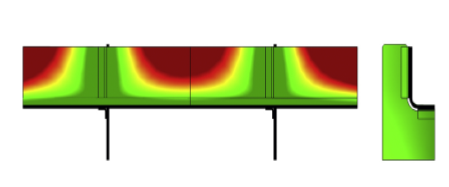