Cellulose nanocomposites – unique effects from nanostructure
Project description
Polymer matrix composites based on fibrous nanoparticles offer interesting properties and are relevant for a wide range of applications. The extent of nanoparticle dispersion is one of the key challenges, which influences the properties of the final material. However, there are many practical problems to solve in order to prepare nanocomposites with nanoparticles individually dispersed in the matrix. This project aims to prepare and characterize materials with controlled nanostructure, resulting in unique material properties. Special emphasis is on connecting the material structure at nanoscale to relevant material properties, and identifying unique features with nanostructured cellulose biocomposites. The effect of CNF dispersion is studied and the macroscopic properties are related to the structure at several length scales. High resolution microscopy (SEM, TEM), uniaxial tensile and dynamic mechanical testing, dynamic vapor sorption (DVS), digital image correlation (DIC), spectroscopic techniques (FT-IR), among others, are tools used to establish the structure-property relationships. Below are some examples of the results.
Moisture resistant and ductile biocomposites
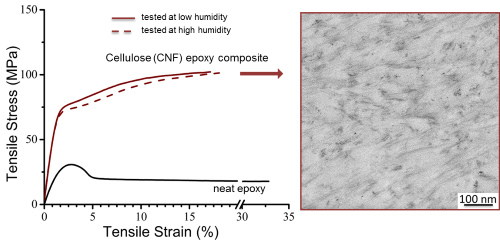
Stress strain curve of pure epoxy (black curve) and CNF reinforced epoxy composite tested at low humidity (solid brown lines) and at high humidity (dashed lines). The right figure is a cross section (obtained from TEM) of the CNF/epoxy composite where CNF fibrils (black lines) are well dispersed at the nanoscale.
High moisture sensitivity of cellulose composites is a major drawback, and has restrained the potential application of these materials. In this work, the moisture problem has been addressed by designing truly nanostructured materials where the CNF fibrils are well dispersed in an epoxy matrix at the nanoscale. This combined with covalent linking of cellulose surface hydroxyls with the highly reactive epoxide moieties leads to materials wich can be virtually insensitive to moisture. The strong increase in strength and stiffness, while retaining the ductility are also important characteristics of CNF-epoxy biocomposites. Control studies with different resins were carried out to clarify the role of nanoscale fibrils, and fibril surface reactivity for hygromechanical properties of the materials.
References:
Nanostructured biocomposites based on unsaturated polyester resin and a cellulose nanofiber network
Farhan Ansari, Mikael Skrifvars and Lars Berglund
Composites Science and Technology 2015, 119, pp 298-306
Cellulose nanofiber network for moisture stable, strong and ductile biocomposites and increased epoxy curing rate
Farhan Ansari, Sylvain Galland, Mats Johansson, Christopher J. G. Plummer and Lars A. Berglund
Composites. Part A, Applied science and manufacturing 2014, 63, pp 35-44
Well-dispersed cellulose nanocrystal (CNC) composites

In this work, environmentally friendly surface modification of cellulose nanocrystals (CNC) was used to prepare nanostructured composite with individually dispersed CNCs. The effect is that the modulus and strength of the composite increase dramatically (solid red line) when compared to composites with unmodified crystals (dashed red line) and the pure polymer reference (black line). One reason for the strong improvement is the presence of extremely well dispersed nanocrystals in modified CNC composites (top right SEM figure), whereas the crystals appear aggregated in the unmodified CNC composite (bottom right SEM figure). Most likely, the majority of published studies are on polymer matrix CNC composites with poorly dispersed CNC particles. Detailed investigations revealed that three major factors contribute to observed reinforcement effects – a) mechanical reinforcement of PVAc by rigid CNC particles (classical mechanism) b) better dispersion provides better reinforcement since individual CNC’s reinforce more efficiently than agglomerates, c) the high surface area created by well dispersed nanofibrils, combined with the compatible interface modifies the intrinsic polymer matrix structure and accelerates physical ageing. The CNC particles promote physical ageing, which leads to a stiffer/stronger PVAc matrix and improved composite properties.
Reference:
Strong Surface Treatment Effects on Reinforcement Efficiency in Biocomposites Based on Cellulose Nanocrystals in Poly(vinyl acetate) Matrix
Farhan Ansari, Michaela Salajková, Qi Zhou and Lars A. Berglund
Biomacromolecules, 2015, 16 (12), pp 3916–3924
Pulp fiber composites with hierarchical structure
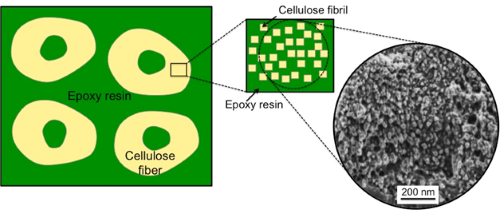
Sketch showing the structure of biocomposites with cellulosic pulp fibers in epoxy. The inset figure depicts that the resin has impregnated the fiber cell wall itself, and surrounds the individual nanoscale fibril aggregates. The SEM image (circle) of the composite cross section verifies this - the details inside the fiber cell wall observable, where individual fibril aggregates (at the nanoscale) appear to be well impregnated and integrated with the epoxy resin.
In this work, macroscopic cellulose pulp fibers (with diameter ~ 30 µm and a length of several millimeters) were used to prepare nanocomposites and utilize the inherent nanostructure of the fiber cell wall. The ’processing advantages’ of a macro sized object were combined with ’property advantages’ of a nano sized object. The designed composites had two scales of reinforcements – the cellulose fibers acting as reinforcement in epoxy matrix (scale of ~30 µm) and, the cellulose fiber cell walls themselves were nano-composites (scale of 20 nm) where the resin had bonded the cellulose nanofibrils together by penetrating into the cell wall. These “composite” pulp fibers provided more efficient reinforcement than “pure” pulp fibers. This is certainly related to improved fiber-matrix interfacial adhesion, but intrinsic fiber failure properties may also be improved.
Reference:
Hierarchical wood cellulose fiber/epoxy biocomposites – Materials design of fiber porosity and nanostructure
Farhan Ansari, Anna Sjöstedt, Per Tomas Larsson, Lars A. Berglund and Lars Wågberg
Composites Part A: Applied Science and Manufacturing 2015, 74, pp 60-68