Sensors improve life for amputees
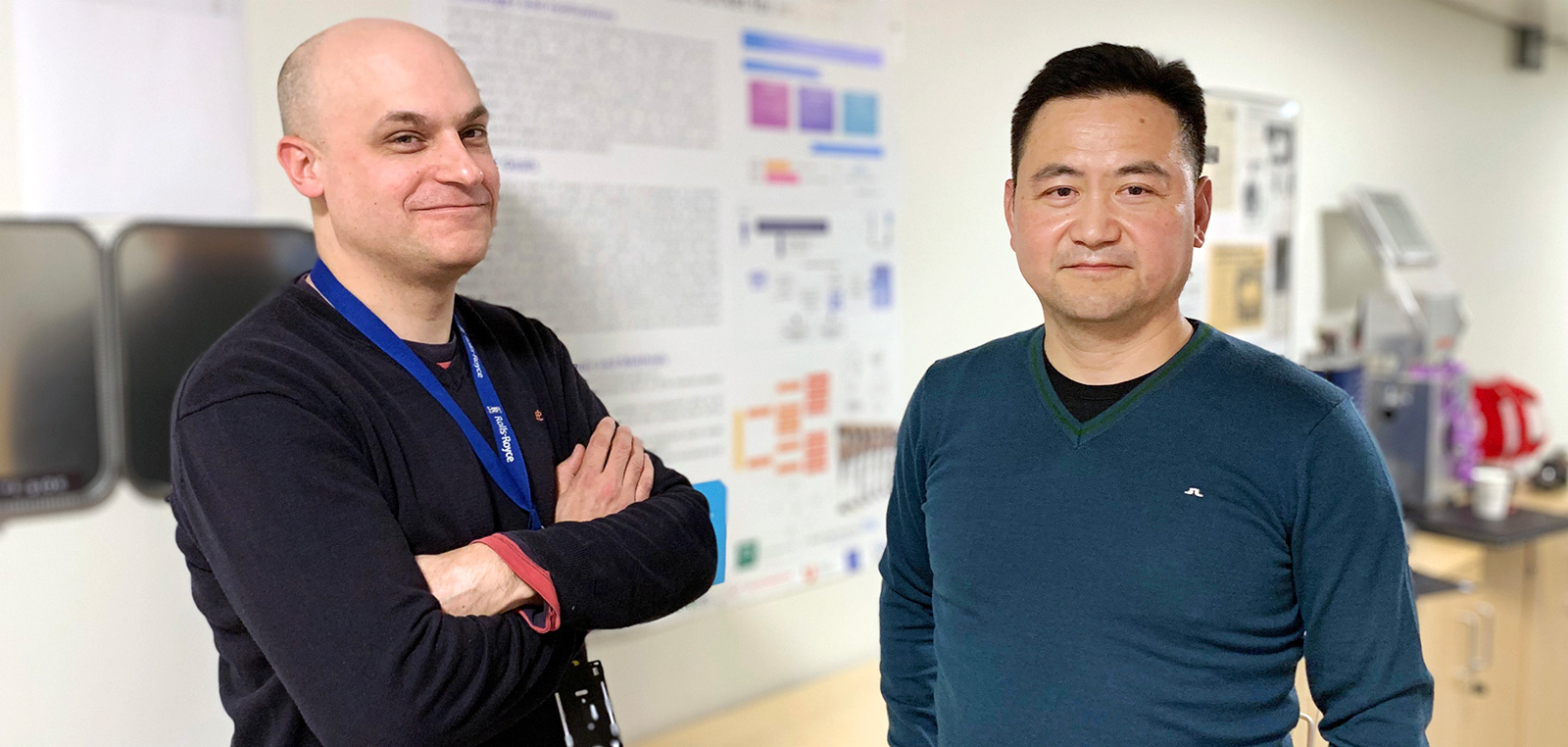
35 percent of the amputees reject prosthetics because they are too uncomfortable. By placing connected sensors in the prosthetic sockets, KTH will optimize the users' prostheses and also save large societal costs.
Around 40 million people in the world have amputated a part of their body. In our part of the world a lost limb is often caused by an accident or a consequence of for example diabetes. We also have a widespread access to substitutes, ie prostheses. But prosthetics are only moderately popular. It’s not the prostheses themselves that are problematic, but the socket that is attached to the residual limb. The size of the stump vary over the day, and a socket will eventually result in a poor fit. The pressure can lead to complications, and chafing from friction can cause severe wounds. In other words, optimizing a prosthetic socket is tricky and around 35 percent of the amputees reject their prostheses due to comfort issues.
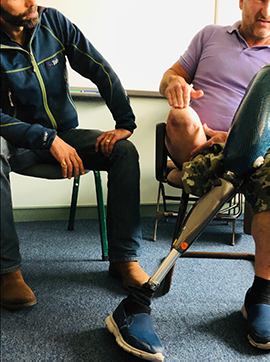
But what if a physician was able grab an iPad and get real-time information about the dynamic conditions in a patient's prosthesis during a day and get an assessment of where the risks of malfunctions and injuries are? Then the doctor could book an appointment before the prosthesis becomes a problem. And at best, the physician’s team will already have been able to develop a new, optimized prosthetic socket in time for the visit.
This is exactly what Dejiu Chen and his colleagues at KTH are developing: an intelligent system that monitors the conditions in the prosthesis socket.

“We integrate small, soft and flexible sensors around the socket, called wearable electronics, which monitor and report what’s happening in the socket, and how the leg moves during a day. The information will result in a three-dimensional map of the dynamic conditions of the socket - in real time. Easily put: Internet in the prosthesis”, says Dejiu Chen at the Department of Machine Design who coordinates the Socketsense team.
The sensors themselves make no assessments, they only send data. The assessments are made by algorithms that estimate the conditions in the socket and the risk of complications.
“AI technology will learn patterns upon which the automated decisions are made. One challenge here is to formalize knowledge and make the correct assumptions. What combinations of data that will be of interest?”, explains Dejiu Chen.
When the algorithms have identified critical clinical parameters, an alert is sent to the healthcare clinic that can act on the information.
But there are more challenges in the project than the assessments, says Dejiu Chen and his colleague Fredrik Asplund, who normally work more towards the automotive industry than biomechanics:
“The sensors mustn’t weigh too much, they mustn’t affect the prosthesis and they have to withstand the body's moisture and heat”, says Fredrik Asplund.
The Socketsense project is a multidisciplinary project funded by the EU. Nine partners - from health care providers and universities to prosthetics manufacturers - participate. The idea is that the project will result in a prototype product to be used in a clinical trial in 2022.
“It is motivating to work in a project with great social impact and where you’ll be able to save large social costs. For the same reason, it is a project that EU keeps its eyes on”, Dejiu Chen concludes.
Text: Anna Gullers