Wafer-scale packaging of RF MEMS devices by patterned, full-wafer adhesive bonding
Patterned polymer layers used as adhesive bonding layer create cavities between two bonded wafers. This technology was initially developed for wafer-scale packaging of RF MEMS devices.
The Microsystem Technology group has been working in adhesive bonding for many years and this knowledge has been used in the activities to package MEMS structures on wafer level.
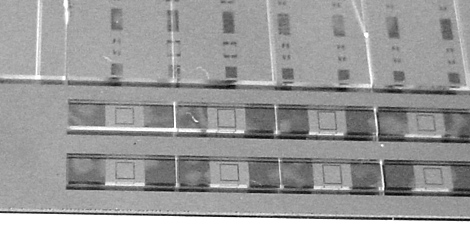
Wafer-level packaging is regarded as a key-technology in solving the “packaging bottleneck” much MEMS projects suffer due to packaging costs of up to 95% of the whole device costs. The Microsystem Technology group is focusing on wafer-level packaging by using a patterned adhesive layer. The main advantage of this method is that the cavities housing the MEMS devices can be created directly in the bonding layer [1].
In contrast to conventional adhesive wafer-level packaging method, where each device is packaged with an individual cap in a flip-chip like way, the MST group developed a technique which allows the parallel packaging of all devices by one full-wafer bonding step. The separation of the capping lids is done afterwards by dicing, together with or separate from the substrate wafer.
To electrically connect such packaged devices, thick film in-plane interconnections through the polymer sidewall where utilized as well as through wafer vias by using a novel two-step etch-technology, based on powder-blasted recesses in the back-side of the glass wafers.
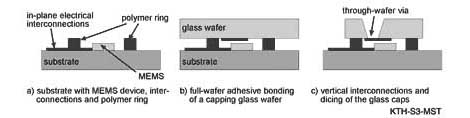
The figure gives a rough overview of the fabrication procedure of wafer-level packaging by full wafer bonding with a patterned adhesive layer, including in-plane interconnections through the polymer wall and vertical interconnections through the capping glass wafer.
Benzocyclobutene (BCB) is the polymer mainly used for the bonding experiments. The MST-group characterized the bond interface by doing Scanning Acoustic Microscopy and tensile strength measurements, in a collaboration with Ericsson Core Production, Kumla, Sweden, and Chalmers University of Technology, Gothenburg, Sweden. Since polymers do not provide full hermeticity, the Microsystem Technology group also looked into techniques to seal such packages by using an additional cladding layer [3].
The recent efforts in patterned adhesive packaging of MEMS devices are to improve the bond strength of pre-cured polymer materials. The MST group has developed and investigated a method to significantly increase the bond strength by using both a rigid and a liquid polymer phase [4].
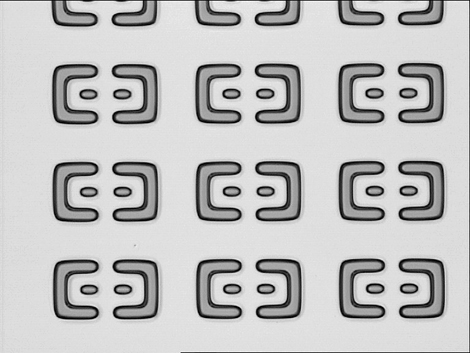