Doktorand byggde unik provnings- anläggning
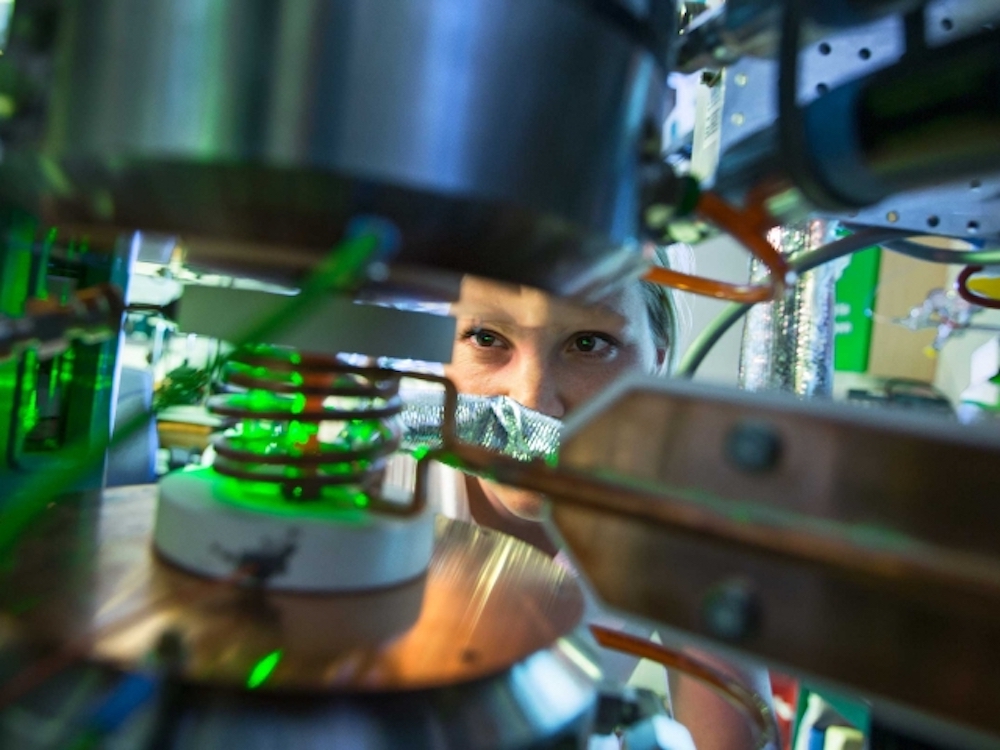
Ingenstans kunde Madeleine Ekström hitta den provningsanläggning hon behövde för sitt doktorandprojekt. Då beslutade hon sig för att bygga den själv – det kan väl inte vara så svårt, tänkte hon. Projektet visade sig vara minst sagt komplicerat, men nu är riggen på plats.
En liten grön ljusstråle indikerar att lasern som mäter töjningen är igång. Temperaturen är inställd på 700 Celsius. Provningsanläggningen här, i ett labb på Materialforskning, är unik, den första som erbjuder möjligheten att göra högtemperaturstester i andra gaser än luft. För dagen testas ett gjutjärn i argon.
– I det här projektet tittar vi mest på gjutna komponenter, det är tre olika material av gjutjärn och stål som jag testar för Scanias räkning. Men man kan använda den här riggen för andra komponenter också, förklarar doktoranden Madeleine Ekström.
Hennes projekt syftar till att ta fram alternativa material till grenrören i Scania-lastbilarnas avgassystem. Materialen måste tåla belastning vid mycket höga temperaturer och samtidigt ha hög motståndskraft mot korrosion. Att bara göra högtemperaturstester i luft är alltså inte tillräckligt, materialen behöver även testas i en mer verklighetstrogen miljö.
– I avgasrör är det ju inte så mycket ren luft. Vi vet att avgaserna gör att livslängden förkortas men frågan är hur mycket, förklarar Madeleine Ekström.
– Förhoppningen är att man ska kunna använda sig av de här måtten vid design av nya material, säger Madeleine Ekström.
Ursprungligen fick hon projektpengar från Vinnova för att genomföra de tester hon ville hos något provningsinstitut. Problemet var bara att det inte fanns något institut, vare sig i Sverige eller i övriga Europa, som åtog sig uppdraget. Ingen hade en sådan provningsanläggning som behövdes.
Då föreslog Madeleine Ekström och hennes handledare på KTH, Stefan Jonsson, att de skulle göra testerna själva. Vilket innebar att de också måste bygga den nödvändiga testriggen. – Jag tänkte att ”äsch, det kan väl inte vara så svårt”. Och vi var bägge lite förvånade över att ingen tidigare hade satsat på en sådan här rigg, Men när vi började bygga den insåg vi varför…
För att genomföra de planerade testerna behövdes en rigg med en gastät kammare där provet kunde utföras. Gasen måste kunna bytas ut, sammansättningen kontrolleras och temperaturen regleras upp till 1000 C. Det var många detaljer som skulle stämma.
Det gick heller inte att använda något metalliskt material till kammaren eftersom den då skulle ta upp induktionsvärme och påverka omgivande delar i utrustningen, till exempel tätningar, negativt.
– Det allra svåraste var att få till en gastät kammare samtidigt som man ska ha något som rör sig i och ur den.
Madeleine Ekström fick prova sig fram för att hitta lösningar på problemen. Det blev många och långa diskussioner med olika leverantörer för att hitta rätt komponenter.
– Ganska mycket inom mekanisk provning finns att köpa färdigt men gassystem och kammare fick vi själva bygga.
Efter ett år av utmaningar och hårt arbete står äntligen provningsriggen på plats, testad och klar. Madeleine Ekström riktar laserstrålen som mäter töjningen.
Delarna till riggen plockades ihop från olika håll, styrsystemet kom från Sverige, en syre-sond från Tyskland, flödesmätaren och andra delar till gassystemet från en holländsk firma. Gaskammaren byggdes av två keramiska plattor och flera olika keramiska material provades innan det blev rätt.
Det tog ett år att bygga provningsriggen men nu står den där, och strax före sommaren kunde de första testerna köras.
FAKTA
Testriggen Corrosion Fatigue Lab
Provningsanläggningen ingår i ett tvåårigt industriprojekt med syfte att undersöka effekterna av korroderande avgaser på nya materialalternativ. I projektet medverkar förutom Madeleine Ekström handledare och professor Stefan Jonsson, biträdande handledaren Peter Szakalos och Scanias projektledare, Baohua Zhu. Testriggen har kostat 1, 6 miljoner att bygga.
Text Ursula Stigzelius
Foto Håkan Lindgren
KTH Magazine 01 JULI, 2014