A 3D printed laser demonstrates new optic manufacturing method
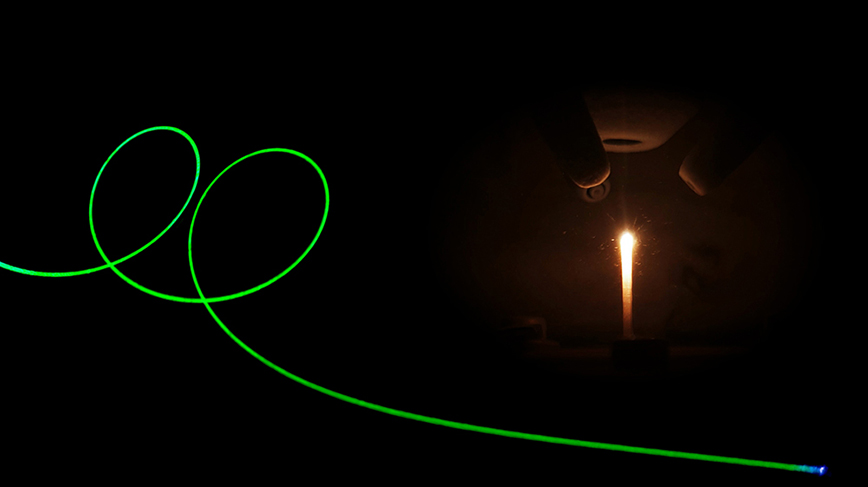
The first 3D printed laser has been produced by researchers in Sweden to demonstrate a sustainable method for manufacturing the next generation of optical fiber components.
Developed at KTH Royal Institute of Technology, the technique could reduce costs and shorten production cycles for small-form, tailored fiber optics, while avoiding the environmental impact of standard fiber manufacturing methods.
“This new method opens the door to manufacturing optical fibers and lasers at a much lower cost,” says Pawel Maniewski , one of the researchers behind the new manufacturing method.
The prevailing method for manufacturing fiber optics typically requires large facilities where toxic chemical reactions are employed to preform pure glass, and multi-story towers are needed to draw the glass into fibers at temperatures of 2,000C.
“All this infrastructure is fine when one wants to produce kilometers of internet cable, but obviously it’s not economically reasonable for a few meters of highly sophisticated fiber, that would be tailored to a unique application,” he says.
Reporting in the journal Optica, Maniewski says that the researchers’ method of “Laser Powder Deposition” produced an Erbium-doped fiber to demonstrate “the ultimate proof-of-concept”. But the method can be readily applied to other materials, making the development of new lasers faster and cheaper, he says.
“Our work is a breakthrough,” he says. At KTH the researchers use an approximately 1.5-cubic-meter 3D printing system and a laser-based lattice tower a few meters high, Maniewski says. “With non-toxic glass powder, we can produce high quality glass fibers which can easily be used as for fiber-based lasers, among other things,” he says. “The entire production cycle can be as short as a few hours, and 3D printing of highly customizable glass takes only a few seconds.”
The method can be used to quickly test new materials and different designs. And its use is not limited to a single material or business area.
“Areas that could be positively impacted by this technology and method are the development of better fiber sensors for health monitoring and better lasers, and new composite materials,” he says. “The latter industry alone has a turnover of more than $93 billion annually."
Peter Ardell/
David Callahan